Technology often gets all the credit when it comes to predictive maintenance. That’s unfair. Technology is important, but it’s only a small piece of a great predictive maintenance program.
The organizational culture has to be right. New processes need to be tested and refined. Data needs to be expertly managed.
In short, the journey to predictive maintenance is slow, but worth it, if it’s done right. Maintenance Holding BV is the right partner is doing and achieving this. Maintenance Holding BV is the missing link in your Predictive maintenance programs.
The six pillars of a predictive maintenance program
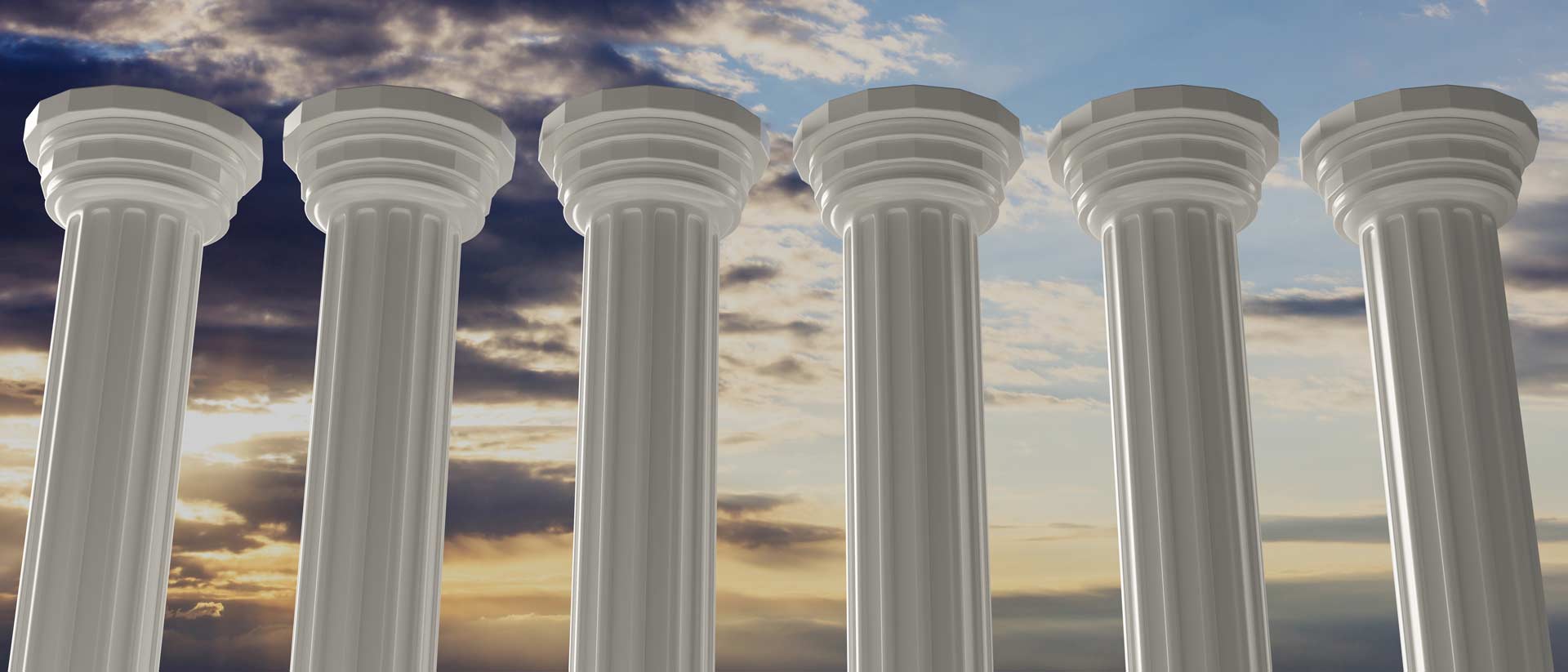
Data
The link between past, present and future
A predictive maintenance program needs a lot of information to be successful. Without the data, you can’t predict anything. If you don’t have a baseline about what’s normal for a pump or a conveyor, you can’t identify or predict anomalies.
Processes
A steady hand on the predictive maintenance ship
Simply put, your processes are the way you work—how your maintenance team plans and does the things it needs to do every day to be successful. An effective predictive maintenance program helps make your whole operation predictable so it can maximize everything from working hours to asset performance.
Tools
Trusty sidekicks ready for the spotlight
Tools and parts play a huge role in allowing predictive maintenance to go from a far-away dream to a realistic goal. Predictive maintenance isn’t new. The difference between 20 or 30 years ago and now is that we have the tools and understanding of parts to do it better and at a lower cost.
Equipment
Not all machines were made for predictive maintenance
Anyone who says reactive maintenance can be totally eliminated has never had their windshield cracked by a stray pebble. While this isn’t exactly an on-the-job example, the lesson still applies to the shop floor: You can’t anticipate everything.
Technology
The glue that keeps the other elements together
Technology is like a dash of salt in a predictive maintenance program—it ties the other ingredients together and makes them shine. It helps you manage, facilitate, and optimize the other pillars of predictive maintenance.
People
Culture and strategy people are key in you program
The long journey to predictive maintenance always starts with people.
It doesn’t matter if your predictive maintenance plan looks good on paper, if you don’t have buy-in from the people who are doing the work.
Proactive maintenance is one highly effective but overshadowed generic maintenance strategy, which when effectively implemented, is significant in improving equipment reliability. Many maintenance teams tend to follow a reactive maintenance approach, due to its low initial costs and low requirement for planning. After all, it’s easier to do nothing than something. Unfortunately, a “fix it when it breaks” approach sends technicians scrambling, and often results in overtime, high repair costs, lost production, and severely reduced asset life. These consequences run counter to an organization’s goals of asset availability and profitability.
Types of Proactive Maintenance
There are many types of proactive maintenance:
Planned Corrective Maintenance (CM)
Maintenance that is required to restore an asset to optimum or operational condition, but does not need to be performed immediately. Planned corrective maintenance occurs when a maintenance need is expected, allowing you to schedule corrective action ahead of time.
Preventive Maintenance (PM)
The most common type of proactive maintenance. Preventive maintenance is scheduled using time-based or usage-based intervals.
Condition-based Maintenance (CbM)
Maintenance carried out when an asset’s monitored condition reaches an unsatisfactory level. Using real-time condition data, maintenance can be performed before failure occurs.
Predictive Maintenance (PdM)
Maintenance scheduled using predictive analysis, based on an asset’s monitored condition, historical performance data, and advanced analytics. Predictive maintenance forecasts when failure is likely to occur, allowing maintenance teams to take preventative action.
How to Implement a Proactive Maintenance Strategy
Once sufficient asset and historical maintenance information is collected, you can proceed with implementing your proactive maintenance strategy. The following steps provide a framework to help your implementation go smoothly.
Energy Programs
At its core, energy conservation is the practice of using less energy in order to lower costs and reduce environmental impact. This can mean using less electricity, gas, steam or any other form of energy that you get from your utility and pay for. With finite energy resources available on our planet, actively conserving energy when possible is beneficial individually and to our larger energy systems.
Energy conservation vs. energy efficiency
While energy conservation is the practice of trying to use less energy for cost and environmental reasons, energy efficiency means using specific products designed to use less energy. These two concepts are inherently similar but involve different methods. It is not only about saving energy, also about safety.